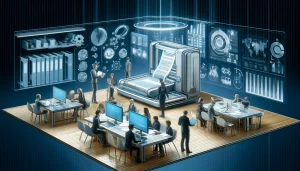
Scanning & Audit
Web and server scanning and audits involve assessing the security and performance of websites and servers to identify vulnerabilities, weaknesses, and potential risks. Here’s an overview of the process:
A Warehouse Management System (WMS) is a software application that helps organizations efficiently manage and optimize warehouse operations, including inventory management, order fulfillment, and warehouse processes. Here are the key components and functionalities typically found in a warehouse management system:
Track inventory levels, stock locations, and movements within the warehouse.
Assign unique identifiers (e.g., SKUs, UPCs) to products for accurate inventory tracking.
Monitor stock levels in real-time and automate replenishment processes.
Receive incoming shipments from suppliers and verify the accuracy of received items.
Generate receiving documents (e.g., packing lists, receiving reports) and update inventory records.
Assign storage locations for received items based on storage capacity, product characteristics, and picking priorities.
Optimize putaway processes to maximize space utilization and minimize travel distances.
Direct putaway tasks based on factors such as storage availability, product dimensions, and picking locations.
Use automated storage and retrieval systems (AS/RS) or warehouse robots for efficient putaway operations.
Manage customer orders, including order processing, picking, packing, and shipping.
Consolidate multiple orders into picking batches to optimize picking efficiency.
Prioritize orders based on order deadlines, order types, and customer requirements.
Plan and execute picking operations to fulfill customer orders accurately and efficiently.
Support various picking methods, including batch picking, zone picking, and wave picking.
Streamline packing processes to ensure proper packaging, labeling, and shipment preparation.
Generate shipping labels, packing slips, and shipping manifests for outbound shipments.
Coordinate carrier pickups and schedule outbound shipments for delivery.
Receive returned items, process returns, and update inventory records accordingly.
Design and optimize warehouse layout for efficient storage and retrieval operations.
Define storage zones, aisles, racks, and bins to organize inventory logically.
Use slotting optimization algorithms to assign storage locations based on product characteristics, turnover rates, and picking frequency.
Implement barcode or RFID technology for accurate and automated inventory tracking.
Capture and record inventory transactions, including receipts, transfers, adjustments, and cycle counts.
Enable lot tracking, serial number tracking, and expiration date tracking for traceability and compliance purposes.
Conduct regular cycle counts and inventory audits to verify inventory accuracy and identify discrepancies.
Schedule cycle counting tasks based on ABC analysis, inventory turnover rates, and historical accuracy levels.
Use cycle counting software to streamline counting processes, reduce errors, and improve inventory accuracy.
Generate reports and analytics on warehouse performance, inventory levels, order fulfillment rates, and labor productivity.
Monitor key performance indicators (KPIs) such as order cycle time, order accuracy, inventory turnover, and picking efficiency.
Gain insights into trends, patterns, and opportunities for process improvement and optimization.
Integrate with enterprise resource planning (ERP) systems, transportation management systems (TMS), order management systems (OMS), and other business applications.
Collaborate with suppliers, carriers, and trading partners through electronic data interchange (EDI) and API integrations.
Enable seamless data exchange and communication to streamline end-to-end supply chain processes.
Implement security measures to protect warehouse data, sensitive information, and physical assets.
Ensure compliance with regulatory requirements, industry standards, and safety regulations for warehouse operations.
Conduct regular security audits and risk assessments to identify vulnerabilities and mitigate potential risks.
Web and server scanning and audits involve assessing the security and performance of websites and servers to identify vulnerabilities, weaknesses, and potential risks. Here’s an overview of the process:
Setting up, tracking, and reporting with Google Analytics involves several steps to ensure accurate data collection, analysis, and reporting. Here’s an overview of the process:
A Customer Relationship Management (CRM) system is a software solution designed to help businesses manage interactions with current and potential customers. Here are the key components and functionalities typically found in a CRM system: